Ray Rex, CRC-US
No rest for the weary! The current European Chemical Agency’s (ECHA) initiative to create a centralized, harmonized Poison Center Notification (PCN) process for hazardous chemicals will definitely impact coating manufacturers and suppliers of raw materials imported into the EU. Since implementation of these new ECHA regulations has been delayed from January 1, 2020 to January 1, 2021 there is time for importing companies to plan and prepare. What are the risks?
Table 1: Risks Exist for Manufacturers Under the New, Harmonized ECHA PCN Regulations
- A nearly full disclosure of the mixture (formulation) composition is required
- Loss of key intellectual property is a possible consequence
- Non-disclosure is only allowed for substances present below 1% if the substance is not classified
- Non-disclosure is only allowed for classified substances when present below 0.1%
Importers currently must register with and notify to nearly each EU country to satisfy individual, nationally promulgated regulations. This has resulted in duplication of efforts and the need to address dramatically varying country-to-country requirements.
A centralized system will create uniformity and simplify the importer’s notification effort. However, it does create concern regarding Confidential Business Information (CBI). Manufacturers not wishing to share product formulations with importers and/or downstream users (e.g. distributors, representatives, etc.) involved in the process of “placing on-the-market” hazardous chemicals will need to use third-party entities located within the EU to notify.
Background
Since 2009 it has been an obligation of EU companies placing hazardous chemicals on the European market to provide information to officially appointed bodies (OAB) in each member state. In some EU member states, the notification to the OAB is linked with the allowance to use the official emergency response number, as legally required in these countries. Often the member state’s national poison center is to be notified.
Nation-specific requirements, however, have created considerable differences in notification requirements throughout the EU member states. The obligations of importers are contained in Article 45 of the CLP (Classification, Label and Packaging) Regulation (Regulation (EC) No 1272/2008). In the past years, the EU Commission reviewed CLP Article 45 and adopted Regulation (EU) 2017/542 adding CLP Annex VIII to harmonize information requirements and notification formats within Europe.
The holy grail of Annex VIII CLP is the harmonization of the notification content as well as allowing notifications to a central authority and database for EU member state access. Achieving this goal will reduce the notification effort by allowing importers to notify the central authority with common information requirements for all EU member countries.
Table 2: Who is Obligated to Report
- EU Importers and downstream users “placing on the market” hazardous chemicals
- “Placing on the market” is defined in Article 2(18) of CLP as “supplying or making available, whether in return for payment of free of charge, to a third party. Import shall be deemed to be “placing on the market”
The new EU Poison Center Notification regulations and their impact on EU importers is one of the more significant programs being implemented by the European Chemical Authority. The announced one-year delay for implementation is an indication of the complexity of the process. Among these are addressing local language requirements and the state of the IT systems in each country that will be required to implement this effort. This article is intended to highlight key elements of the PCN initiative and identify the potential risks involved as this change in EU regulations moves toward implementation.
As a US company trading with Europe, why should I be concerned?
We are all painfully aware that Europe does not care for the protection of intellectual property when it comes to the safe use of chemicals, and the Poison Center Notification initiative adds more complexity to your efforts to keep CBI as CBI.
As a matter of fact, under the new harmonized notification system, a nearly full disclosure of the composition is required. Non-disclosure is only allowed for substances present below 1% if the substance is not classified and below 0.1% if the substance is classified.
Annex VIII of the CLP Regulations does allow for notifications by a third party/consultant (an EU based company), providing at least some level of CBI protection). The compositional information is kept as a secret by providing to the duty holders (those required to notify) a Unique Formula Identifier (UFI) code. The business significance is that suppliers do not have to share their product formulations with their distributors and/or down-stream users in the EU.
What determines if a mixture is reportable?
The regulations deal with chemicals that are “classified as hazardous based on their health or physical effects.” Environmental hazards do not trigger notification obligations. The criteria for reportable chemicals and mixtures are contained in the CLP Regulations, Parts 2 and 3 of Annex 1.
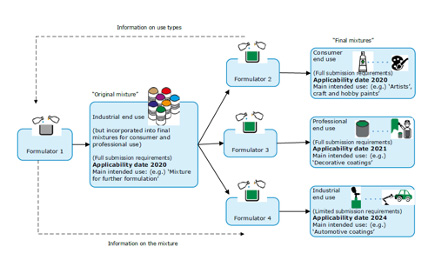
Figure 1: Which Deadlines Apply for Different Mixtures- Alternative Use Types
Certain expectations to the above classifications of mixtures have been identified with regard to reporting obligation deadlines.
Table 3: Some Notable Exceptions to Notification
- “radioactive substances and mixtures […]”;
- “substances and mixtures which are subject to customs supervision, provided that they do not undergo any treatment or processing, and which are in temporary storage, or in a free zone or free warehouse with a view to re-exportation, or in transit”;
- mixtures used in scientific research and development, provided they are not placed on the market and they are used under controlled conditions in accordance with EU workplace and environmental legislation;
- waste; and
- certain mixtures in the finished state, intended for the final user:
- medical products,
- veterinary medicinal products,
- cosmetic products,
- medical devices that are invasive or used in direct physical contact with the human body, and in vitro diagnostic medical devices, and
- food or feeding stuffs
A New Mandatory Label Element – UFI (Unique Formula Identifier)
The UFI is a unique 16-digit code to be printed on or affixed to the label of a product and is an additional means of identifying a mixture. The UFI unambiguously links the submitted information on a mixture (and hence information relevant for emergencies) to a specific product placed on the market. It is generated using the companies VAT number and a 9-digit formulation code.
For some instances (unpackaged goods, purely industrial uses, and some others) it will be sufficient to list the UFI within the products SDSs. Although it is not currently legally required, the author of this article believes that most, if not all classified mixture SDS’s will contain the UFI in the future.
What Information needs to be provided (Annex VIII Part B)?
Table 4: List of Information that Needs to be Reported
Part B.1
- Product Identification
- UFI (Unique Formula Identifier)
- Trade names
- Submitter Details
- Name, address, etc.
- Matching information on the label
- Details for rapid access
- Only for Industrial mixtures with reduced informational requirements
Part B.2
- CLP classification of the mixture and label elements
- Toxicological Information
- Of mixture or components
- Full content of SDS Section 11
- Additional Information
- Type and size of packaging
- Colors physical state of the mixture as supplied
- pH value, where applicable
- Product categorization (according to EuPCS)
- Use types (consumer, industrial, professional)
Part B.3
- Full composition
- Substance name and CAS or EC number
What can you do?
Proactively review your product lines and identify the classifications (according to Europe’s CLP) and end-users for each product. Create a hit list in advance for each deadline to better understand resource needs for implementation and prevent last-minute notification efforts. Communicate with your EU based clients and start drafting a strategy for future product compliance. Avoid notifying the Phase 1 products during the 2020 Christmas week; your customers and EHS personnel will appreciate your proactive management.
Chemical Regulatory Compliance, d/b/a CRC-US, (www.crc-us.com) is a sister company of CSB GmbH, a 28-year old company started by Heinz Dobbertin and now managed by Lars Dobbertin, is focused on serving all phases of the global chemical industry with regulatory and compliance services. CSB GmbH has full coverage and expertise for all REACH related activities and only representative (OR) services located in the UK and the EU 27. Ray Rex, President of the CRC-US, has over 30 years of experience in the specialty chemicals market including the paint and coatings market as the former Commercial Director of HALOX. (ray.rex@crc-us.com)
CRC-US supports the CHEMARK Consulting Group, Inc. in providing strategic direction for marketing products around the world.